In the world of process engineering, the ability to escalate lab-proven chemistry to industrial magnitude is of immense significance. Morteza Hadian and his team use computer simulations to potentially transform large-scale industrial applications. What if the chemistry perfected in the lab can be scaled up for use in major industries?
In May 2023, PhD student Morteza Hadian is eager to show his supervisor Kay Buist a remarkable finding in his research/work. Morteza and his team, who work at TU Eindhoven, observe patterns of yield over time. This means that they track how much product is produced in their experiments as time goes on. This is what Morteza tried to simulate in his models, which he had done surprisingly well in one of the first tries. In other words: he managed to predict what was about to happen in the reactor without actually running it, using his models.
So, to Morteza’s surprise, the computer simulation shows remarkably similar patterns to the real world. This alignment, though theoretically expected, is surprising in its level of detail. To a layperson, this might not immediately sound exciting, but to Morteza, it definitely is. "Imagine inputting letters into a model because you want to make sentences, only for the machine to produce a poem," he says.
“Think of it like playing with numbers to understand how things happen inside the reactor.”
For the past four years, Morteza and his team have been working on the thermocatalytic decomposition of methane. It’s all part of ‘greenifying chemistry’. But rows upon rows of data, charts, statistics, and a diligent observer trying to decipher it all in a simulated environment – those might not be the first things that come to mind when thinking of a sustainable chemical industry. Yet, for the past four years, this has been the most of Morteza and his team's daily grind.
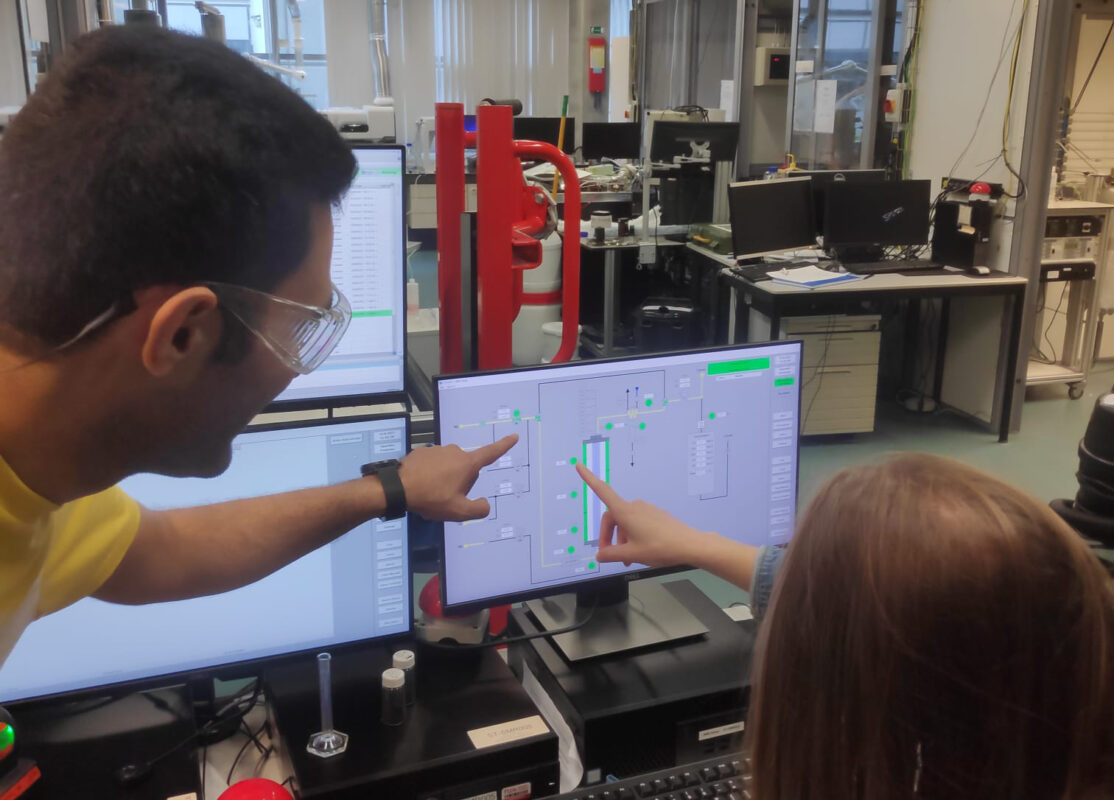
In their project, they work with a reactor that turns methane into hydrogen and carbon materials. “We put natural gas into it and get hydrogen out from the top,” Morteza explains, “while also keeping an eye on carbon fiber forming inside the reactor. We conduct experiments and learn from them and then use computer simulations to learn this process more, and predict its result in different conditions.”
Think of it like playing with numbers to understand how things happen inside the reactor. They also break the reactor down into smaller pieces, like tiny building blocks, to learn how it works and what happens to the materials inside different blocks. In this way, Morteza and his fellow PhD students have been exploring an elaborate cascade of 'what-ifs'. What if we adjust the temperature? What if we fiddle with the catalysts? What if we alter the reactor's conditions or its design — how would that affect its performance? What if we change the materials we work with? What if we can refine processes and products to make them more efficient, cost-effective, and environmentally friendly?
In the world of process engineering, these scenarios hold immense significance. Because the big question looms large: What if we can take the chemistry we’ve perfected in the lab and scale it up for use in large-scale industries?
Within ARC CBBC, Morteza collaborated intensively with Suzan Schoemaker and Tom Welling from Utrecht University, as well as industry experts. They worked together in a so-called ‘multilateral project’, where multiple researchers from different universities and companies work together on a project. Suzan explains: “We work on the same reaction, but we work on it on different scales. Morteza works more towards an industrial scale, while we work on a fundamental lab scale. We really try to look in the details of what happens on the smallest scale.”
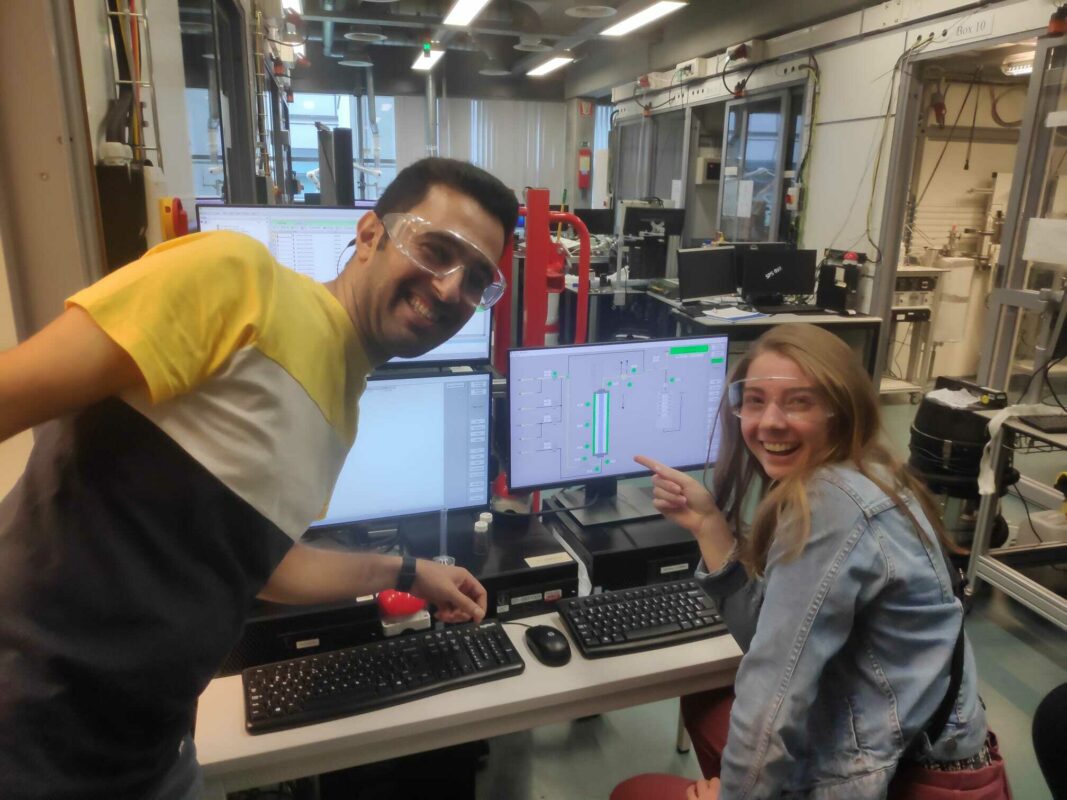
Their project was focused on sustainably producing hydrogen from methane, avoiding CO2 emission in this process. Hydrogen is an important fuel for industry, and increasingly so in the rest of society. But, the conventional method of producing hydrogen, so-called grey hydrogen, produces CO2 as a by-product.
Instead, this multidisciplinary team tried to find a good way to produce valuable carbon materials as a by-product. Carbon fibers, more precisely. These fibers have the convenient characteristic of being both light and strong, making them perfect for use in cars, bicycles, aircrafts or sports accessories. Something way more desirable than CO2, to say the least.
"In the world of process engineering, these scenarios hold immense significance. Because the big question looms large: What if we can take the chemistry we’ve perfected in the lab and scale it up for use in large-scale industries?"
And every researcher in this project played their own role, like a cog in a watch. Suzan: “The idea was that I would find out which catalysts work best, and that Morteza would see how we can scale the production up to larger numbers.” But the collaboration went not just one, but two ways: “I could analyze processes on a small scale, and Morteza at a large scale. We could then compare our results, and see if they are similar and where they differ. Like that, we checked our results with one another and see where we could improve.”
Where Suzan and Tom were more focused on the catalysts, “which, really, are their babies”, as Morteza jokingly says, Morteza himself was more focused on the application. Working with computer simulations means you're navigating many different factors. “For example,” says Morteza, “how gas molecules diffuse into particles, how particles move within the reactor, how temperature changes happen, and how gases flow inside the reactor.”
He goes on to explain that you work on each of these aspects separately, like having all the individual parts needed to build a car: tires, the frame, steering, brakes, you name it. “But having these parts doesn't automatically mean you have a car that's ready to drive – let alone a safe one,” says Morteza. “They all need to be carefully connected and integrated to be able to operate.” And this is what made Morteza’s ‘discovery’ in May so exciting: what he saw in that model, was (by way of speaking) a car that not only operated smoothly, but also had an unexpected but welcome CD-player to boot.
Transforming the chemical industry into a greener, more sustainable one is not done overnight. We can't just pull the plug on the existing system and start anew. That's where computer simulations show their power. They allow scientists to take the complicated aspects of the real world, simplify them into a digital domain, and then use them as important building blocks.
Imagine having to achieve all of this in the physical world – it would demand an incredible amount of time, energy, human effort, and financial resources. Computer simulations not only streamline the path to innovation but also make ‘greenifying chemistry’ an attainable and sustainable reality.
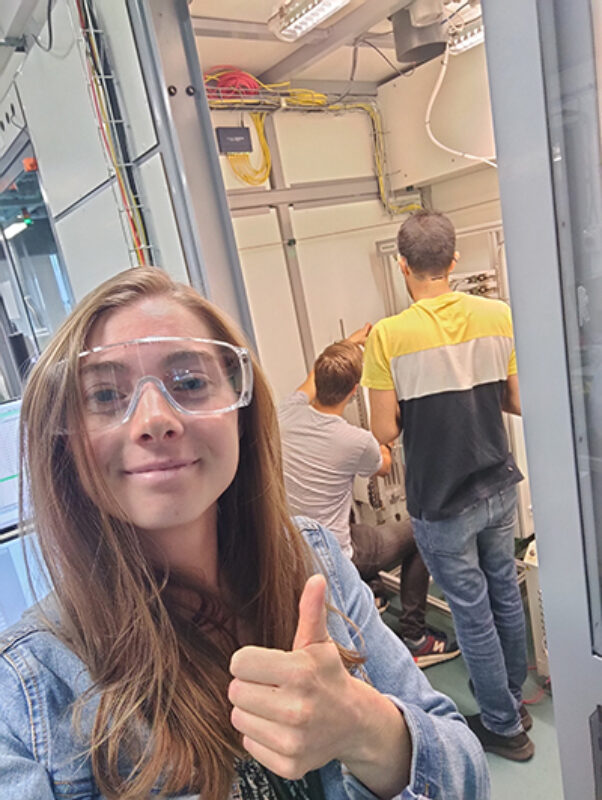
Morteza Hadian concluded his project in June and successfully defended his thesis in October 2023. His promotor was prof. Hans Kuipers. Morteza currently works as a Process Engineer at Avantium in Amsterdam. Suzan will defend her thesis in 2024. The project they worked on will get a sequel within ARC CBBC; in 2024, the multilateral project “Methane Pyrolysis” will be launched on the same topic, building further upon their results.
Morteza and Suzan also made a podcast episode together! You can find it below.