22 March 2022
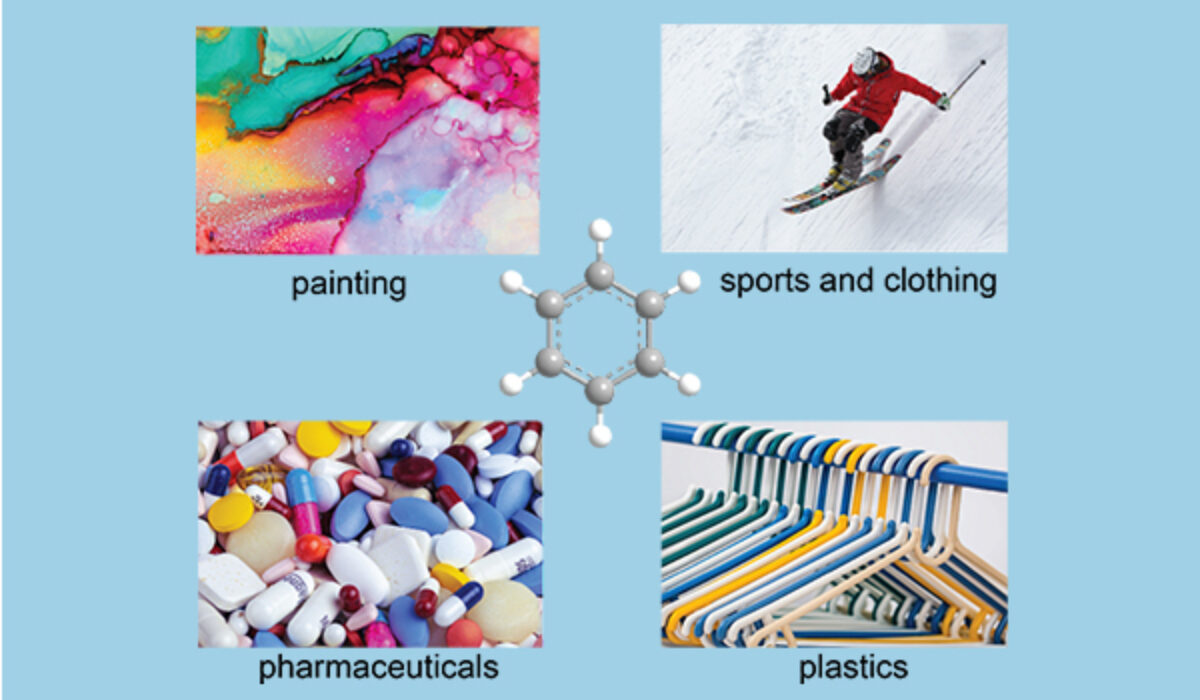
You might be surprised that many items taken for granted in our daily life such as medicine, tennis racquets, or adhesive rely on the products made by the carcinogenic chemical, aromatics. But don’t feel scared, let’s come close to the aromatics industry to learn about its key role in our modern society, including food packaging, painting, cosmetics, and pharmaceuticals. At present to achieve the sustainable economies globally, the aromatics industry becomes more important while its production requires a higher standard.
Since the first evolution by IARC (The International Agency for Research on Cancer, https://www.iarc.who.int/) in 1974, benzene and most aromatics were found to be carcinogenic to humans. Fortunately, these are never the final consumer product. Benzene, toluene, and xylenes (hereinafter, BTX) are the vital compounds that are widely used to produce polystyrene, cumene, and cyclohexane. These are the starting materials to the final products including plastics for packaging, lightweight foam for house insulation, aspirin as daily painkiller, and nylon for sport equipment.
The quality of our life has been dramatically improved thanks to the benefits of aromatic-based products. At the same time, you never worry about your health when you drink Coca-Cola from the one-liter plastic bottle, which is made from hazardous aromatics. That is because the manufacturers implement the more stringent standard than required to protect consumers from any risk of these applications. It is reported that the increasing demand for aromatics-based materials drives the substantial growth of the global consumption of aromatics. Despite the economic recession due to the COVID-19 crisis, this market size is still projected to grow from USD 6.4 trillion in 2019 to USD 7.3 trillion by the end of 2025 at a Compound Annual Growth Rate (CAGR) of 2.22%. Traditionally, the supply of aromatics heavily hinges on fossil fuel, particularly crude oil. Catalytic reforming and cracking of naphtha provide for aromatics by more than 80% of the global production volume. To develop a fossil fuel-free economy, a more sustainable source of BTX is desperately needed.
In this research, methanol is used as feedstock to produce BTX, while the “green” methanol is synthesized from hydrogen and carbon dioxide. The goal of this bilateral project involving BASF, Utrecht University, and Delft University of Technology is to develop a more sustainable methanol-to-aromatics process. Besides the direct relevance to one of the Founding Industrial Partners of ARC CBBC, namely BASF, this research would also provide more insights and clear guidelines on the use of catalysts for other chemical processes. On top of that, this research fits within one of the strategic scientific ambitions of ARC CBBC as it focuses on small molecule activation, in particular methanol.
Solid foundation: get rid of the fossil fuel
Aromatic-based products provide the solid foundation that contributes to the comfort, safety, and security of everyone’s life. Conventionally, the production of aromatics is heavily dependent on the crude oil refinery and cracking. Needless to say, the future society is green. It requires everyday products and aromatics to be produced through a cheaper and more sustainable process. Moreover, the contradiction between mankind’s ever-increasing need for energy and the depletion of fossil fuel resources coupled with the severe environmental issues like pollution and CO2 emissions drives a more sustainable production beyond oil and gas.
In 2016, George Andrew Olah, the Nobel Laureate scientist proposed an innovative economy model in his book, Beyond Oil and Gas: The Methanol Economy: “Methanol, a convenient liquid fuel and raw material for synthetic hydrocarbons, offers an alternative to depleting sources of fossil fuels and can be produced, for example, by reacting H2 with CO2 from industrial effluents or the atmosphere.”
Figure 1. Scheme of future CO2-based chemical industry. Inspired by George Olah.
For nearly 30 years’ research, it has been realized that methanol transformation is a very complicated process. Together with BASF and Utrecht University, we explore a wide range of catalysts in the methanol-to-aromatics process. Their catalytic performances are then evaluated in comparison with the present catalysts under the same conditions. Meanwhile, we apply more local and bulk characterizations including spectroscopy, X-ray diffraction, gas chromatography, and other techniques on these materials. All this collected information will help us to better understand the catalyst-production relationship, which eventually lead to a more sustainable methanol transformation saving energy and decreasing the cost to produce benzene, toluene, and xylenes
Coordinated with the input of the industrial partner BASF and academic partner Utrecht University, we hope our MTA research could help the industry move one more step towards the final industrialization to provide more cheap and reliable aromatic-based consumer products. And we believe the wide use of these products combined with the effective recycling (another research topic) strategy has a huge positive impact on the environment and contributes to a sustainable future.
This work is part of the Advanced Research Center for Chemical Building Blocks, ARC CBBC, which is co-founded and co-financed by the Dutch Research Council (NWO) and the Netherlands Ministry of Economic Affairs and Climate Policy.