19 April 2021
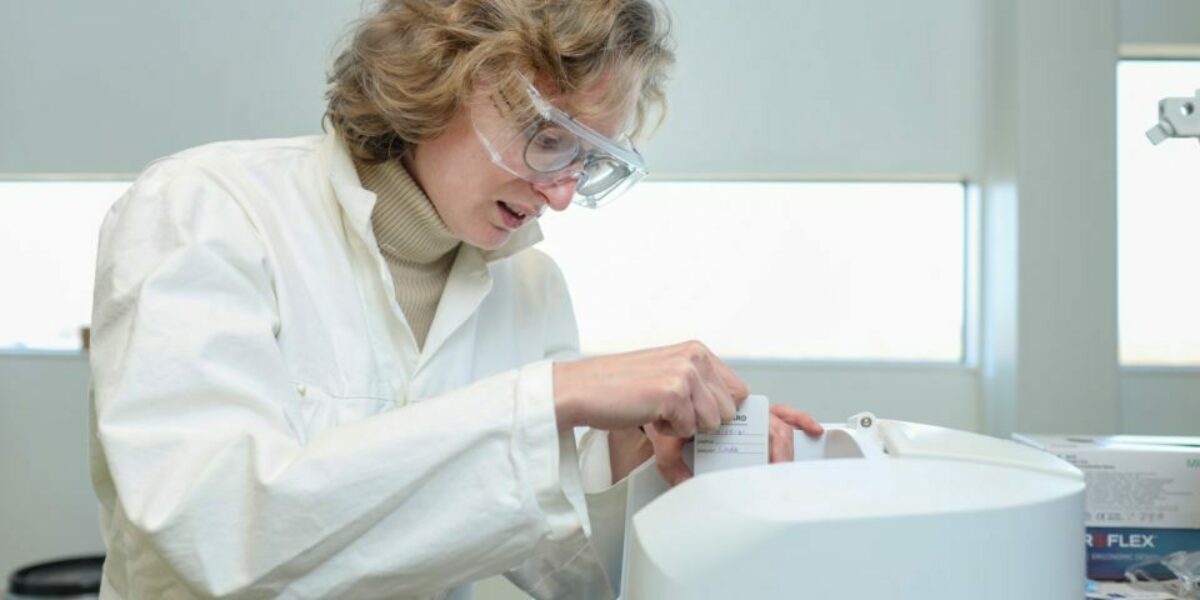
The search for more sustainable paints
Although paint has been around for millennia, there is always room for improvement. Currently, the search is for more environmentally-friendly materials. But chemistry is like cooking: you cannot change the spices and expect the texture and taste to be the same, especially if you don’t know the oven settings. Change the ingredients of a paint is practical only when we understand what is going on inside the can and on the wall.
Next to decoration, paint also functions to protect materials such as wood, steel and concrete from environmental damage. For example, the paint on your window sills protects the wood from sun and rain. Generally, protective paints are referred to as coatings, which cover a material by forming a physical barrier to protect it. Corrosion and corrosion protection are major expenses in industry and infrastructure: in 2002, the estimated cost of corrosion in the USA was $276 billion (276 000 000 000) dollars per year, or 3.1% of the gross domestic product. (http://impact.nace.org/documents/ccsupp.pdf) and it is not likely to be much different in Europe. The need to protect steel from corrosion with a coating is obvious also to those that own an old bicycle.
Over the years, many improvements have been made to the color, drying time, adhesion and other properties of coatings. Increasing world population, climate change and crude oil shortages demand an increase in sustainability in the chemical industry, including the paint industry. Within ARC CBBC, the University of Groningen in collaboration with AkzoNobel, is looking to take paints a step further. We take multiple approaches to make coatings more sustainable: use bio-based starting materials (https://www.eurekalert.org/pub_releases/2020-12/uog-gcc121420.php), use water as a solvent (https://arc-cbbc.nl/projects/crosslinking-in-waterborne-coatings-with-new-building-blocks/) or look at the other components in the paint such as pigments and driers. The search for new driers is my focus!
However, you cannot simply remove a component and replace it with any sustainable one, because a different component has different behavior and will thereby change the properties of the paint. To understand the essential aspects of the current components we need to know what is going on in the materials on a (macro)molecular level. Only if we understand how paints work to form the desired coatings, we can start to look at replacements and see how they affect the properties of the material.
History of paint-improvement
Lead-based pigments, such as lead-white, were used for centuries. They served a dual purpose: not only did they provide whiteness, lead pigments also reduce the drying time and allow you to add a new layer of paint sooner. However, lead is toxic and lead was banned from paint and gasoline. Two different ingredients had to be used to replace lead in paint: a white pigment and component that reduces drying time. This example illustrates that it is not easy to replace a component in paint because many of those components have multiple purposes.
In the 1950s, a new material called vinylester was developed. Mixed with styrene it can form a very effective coating, protecting steel against acidic liquids such as sulfuric acid, beer and crude oil. The mixture is not applied on the outside but on the inside of big containers that you can see near seaports. It can be spray- or trowel-applied and after drying the first layer, usually the process is repeated several times. The drying time of the coating is important: too short and the coating will harden before everything is applied, too long and you have to wait for days before being able to apply the second layer.
My research is focused on the search for alternative driers. But here we run into a problem: we don’t understand well the role of the current drier. Some alternatives have been tried but all failed. The best way forward is to investigate the role the current drier plays in the process.
How to understand what is going on
So how do you look at a drying paint? One way is to check every few minutes if your coating is still sticky. But doing this manually is time-consuming and it is also not very precise: your idea of a dry coating will be different from mine. To improve consistency, we use spectroscopy to look at the coating, and as chemists, we like to look at it on a molecular level.
All chemical bonds in a molecule vibrate. The energy of this vibration is quantized, meaning it has distinct energy levels. Usually, a bond is in the lowest energy level but interactions with light can change this. The transition between the lowest energy level and a higher level is always at the same energy for the same bond. We can use this fingerprint to identify a molecule.
When the molecule changes, the fingerprint changes. The rate of change, as well as the extent, can tell us about the properties of the coating that we have formed. With the current drier, a sturdy but still flexible coating is formed in a few hours. Alternative driers give bad quality coatings: they can be tacky, brittle or non-adhesive. Looking at it in the lab, we see that this is caused by too slow or too fast reactions. The difference in rate of change seems to influence the extent of change, giving different coating properties. The most important thing is to get the timing right!
Painting the future
Every paint is a unique mix of components such as polymer, solvent and drier that determine the properties of the coating. Current coatings have been optimized to serve a specific purpose in a certain environment. Changing one component will affect the performance of a coating. We cannot replace one ingredient and expect the outcome to be the same – we need to change the entire composition. Intuitively we all know this: cooking chicken breast is not the same as cooking a rump steak: different time, different temperature and definitely different herbs and spices!
A truly sustainable coating needs to be people- and environmentally-friendly. The best solution moving forward is not to change the recipe, but use the new ingredients to create a new and improved dish!
The author would like to acknowledge prof. Wesley Browne (University of Groningen), prof. Ben Feringa (University of Groningen), Hugo den Besten (University of Groningen), Keimpe van den Berg (AkzoNobel) and Jitte Flapper (AkzoNobel).
This work is part of the Advanced Research Center for Chemical Building Blocks, ARC CBBC, which is co-founded and co-financed by the Dutch Research Council (NWO) and the Netherlands Ministry of Economic Affairs and Climate Policy.